What Does Premier Aluminum Llc Mean?
Table of ContentsUnknown Facts About Premier Aluminum LlcSome Ideas on Premier Aluminum Llc You Need To KnowA Biased View of Premier Aluminum LlcGetting My Premier Aluminum Llc To Work
(https://profiles.delphiforums.com/n/pfx/profile.aspx?webtag=dfpprofile000&userId=1891251050)Typically, a purchaser's key duty was to discover qualified and receptive distributors. In many cases, buyers assumed that any kind of provider ready to contractually meet the acquisition demand was certified. Using reduced cost and unqualified distributors can create high quality issues, and threw away time and money in the long run. To assist you via the procedure, right here are some things to take into consideration when picking the ideal metal casting distributor.
As an example, a business that just uses the investment casting process will certainly try to offer you on why that process is best for your application. What if making use of the sand casting procedure is best for you and your demands? Rather, seek a vendor that uses a series of casting processes so the very best alternative for YOU is selected
If collaborating with a solitary resource for every one of your casting needs is essential to you, the vendor needs to be varied in its capabilities. When combined with other integrated abilities, this can aid simplify and press the supply base. When picking the appropriate casting distributor, mindful consideration needs to be given to top quality, solution, and price.
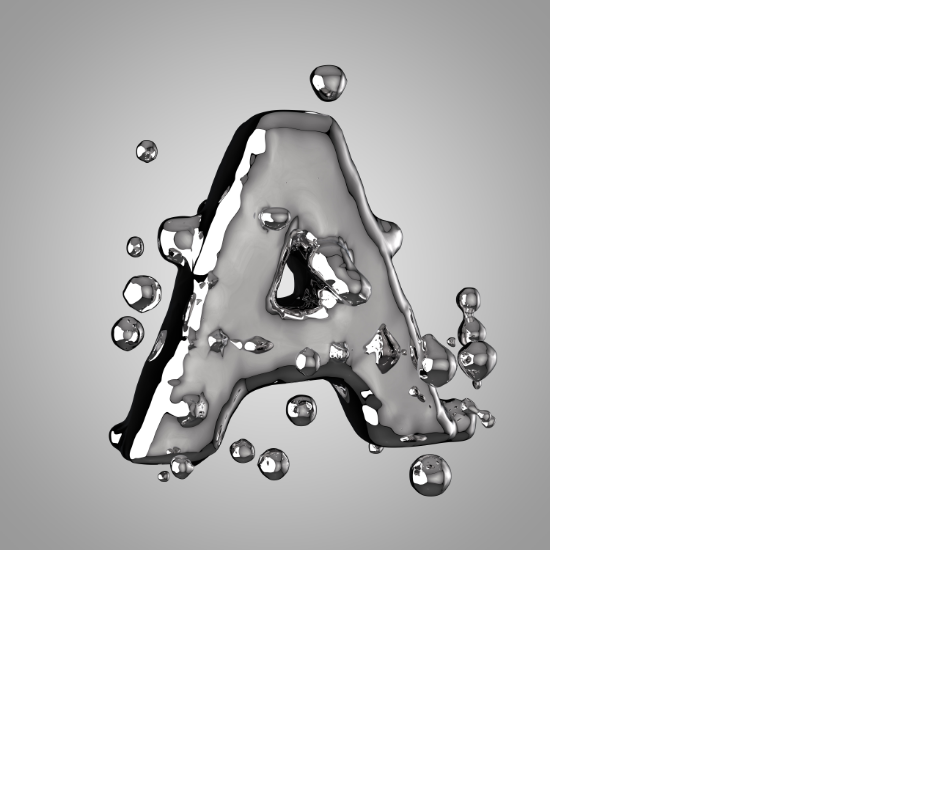
The Buzz on Premier Aluminum Llc
Purchasers progressively select casting distributors who have machining capabilities. If the casting distributor finds a problem throughout machining, the issue is settled much faster with no conflict over whose mistake it is.
What do you require from your spreading distributor? Are you looking for a person to just deliver a steel element to your doorstep or do you need more?
Some foundries are restricted or specialized. Make sure the vendor can fulfill all your product or alloy needs to eliminate the need for multiple suppliers.
3 Simple Techniques For Premier Aluminum Llc

Research the vendor's website. Talk with a sales representative or business partner. Ask a great deal of inquiries. Visit their center. Obtain an understanding of what they can do for you and if you can see yourself developing a strong, mutual partnership with them.
Aluminum is also light-weight and has great rust resistance, making it optimal for applications where weight and resilience are vital aspects. Furthermore, light weight aluminum spreading is a cost-efficient technique of production, as it calls for much less power and resources than other methods. Iron casting, on the other hand, entails putting molten iron into a mold to create a desired shape.
More About Premier Aluminum Llc
Iron spreading is likewise able to endure heats, making it ideal for usage in applications such as engine components and industrial equipment. However, iron casting can be extra costly than light weight aluminum casting because of the higher price of basic materials and the power required to melt the iron. When determining in between light weight aluminum casting and iron casting, it is very important to take into consideration the certain requirements of the application.
If strength and durability are more vital, iron spreading may be the much better option. Other variables to take into consideration include cost, production volume, and lead time. To conclude, both aluminum spreading and iron spreading have their very own unique benefits and drawbacks. By carefully taking into consideration the particular demands of the application, suppliers can select the finest process for their product.ZheJiang Dongrun Casting Market Carbon Monoxide,. Ltd was constructed in 1995, We have remained in the casting sector for more than 25 years. Die casting is the name given to the
procedure of producing complicated steel parts through use molds of the element, likewise recognized as passes away. The process makes use of non-ferrous metals which do not consist of iron, such as light weight aluminum, zinc and magnesium, due to the desirable homes of the metals such as low weight, greater conductivity, non-magnetic conductivity and resistance to corrosion. Pass away casting production is quick, making high production levels of elements simple.
It generates more elements than any type of various other procedure, with a high level of precision and repeatability. To read more regarding die spreading and pass away casting products utilized at the same time, read on. There are three sub-processes that fall under the category of die spreading: gravity die spreading (or permanent mold casting), low-pressure die casting and high-pressure die spreading. The pure steel, likewise called ingot, is included to the heater and kept at the molten temperature of the metal, which is after that movedto the shot chamber and injected into the die. The pressure is then preserved as the steel strengthens. When the metal solidifies, the cooling process begins. The thicker the wall surface of the component, the longer the cooling time because of the amount of interior metalthat likewise requires to cool down. After the part is totally cooled, the die halves open and an ejection device presses the element out. Complying with the ejection, the die is closed for the following injection cycle. The flash is the extra material that is cast during the process. This have to be cut off using a trim tool to
leave simply the main element. Deburring gets rid of the smaller sized pieces, called burrs, after the cutting process. Ultimately, the part is polished, or burnished, to offer it a smooth surface. This proved to be an inaccurate examination, since the tester might reduce into a piece and miss a location with porosity. Today, leading producers use x-ray testing to see the whole interior of parts without reducing right into them. This enables them to much more precisely approve or turn down parts. To get to the finished product, there are 3 primary alloys utilized as die spreading material to pick from: zinc, light weight aluminum and magnesium. Zinc is among the most used alloys for die spreading because of its reduced cost of raw materials.